Position Sensors
AST position sensors are used to detect relative movements between two mechanical components and are adapted to the respective application. In this context, the company uses either 3D Hall or inductive technologies. The stationary part of the sensor interacts with the target mounted to the moving component via a contactless and wear-free inductive or magnetic coupling. The shape of both the stationary sensor component and the target can be adapted to the respective application within wide limits. 3D Hall technology offers multiple benefits resulting from the ability to determine positions in up to 3 axes with sensing ranges of up to 100 mm. The inductive technology reveals its strengths in one-dimensional readings at ranges of up to 500 mm. Both technologies stand out due to the fact that both the stationary and the moving elements of the sensor are encapsulated against environmental influences, thereby enabling use under adverse environmental conditions. In addition to position, the sensor can, of course, also be used to capture derived variables such as velocity or acceleration. Position sensors are used in a wide variety of applications, from measuring brake pad wear in the automotive sector to robot gripper applications to detecting imbalances, e.g., in washing machines.
AST’s force/torque sensors utilize the strain placed on the given mechanical structure by the applied forces and torques. Such strain is measured by the sensor using the differential eddy current principle. In the process, the sensor achieves a resolution in the nanometer range. The existing structural component serves as a reference for the force/torque measurement. The shape of the sensors can be adapted to the conditions of the structural mechanics within wide limits. In most cases, a housing that seals off the structural component protects the sensor against environmental influences up to a rating of IP6K9K. Our force/torque sensors are used, for example, in electrically actuated brakes of electric vehicles or for axle load measurement in commercial vehicles.
All AST sensors are equipped with a microcontroller and are therefore able to execute complex algorithms directly on the sensor. An output signal processed in this way is then made available in analog or digital form.
Wear sensor

Every mechanical assembly sustains a certain amount of wear the longer it is used. This presents itself in a variety of ways, including changes to component geometry and traces of mechanical wear in the form of material deposits on the component surface. These largely undesired changes occur on components such as clutches, transmissions, and brakes.
Wear impairs the function and effectiveness of components, which can lead to serious component damage and subsequent failure. This in turn requires the investment of additional time beyond the scope of the usual service intervals. While this may simply be an annoyance for users of private vehicles, it can cost a significant amount of money for operators of commercial vehicles including trucks and buses. After all, downtime is sure to result in lost earnings. It is therefore necessary to limit wear to easily replaceable components known as wear parts.
As our smart sensors continuously monitor the wear level of safety-related components, and given that we are even able to determine the current temperature on request, we can use corresponding algorithms to issue highly precise predictions of how the operating status will change over time within the assemblies. This therefore enables the individual optimization of service times. For example, our sensors in brake systems can detect whether a brake disc has been warped by thermal overload or whether dirt is limiting the effectiveness of a brake piston. This not only prevents breakdowns and critical driving statuses, it also eliminates the need for regular visual inspection.
Inductive position sensor
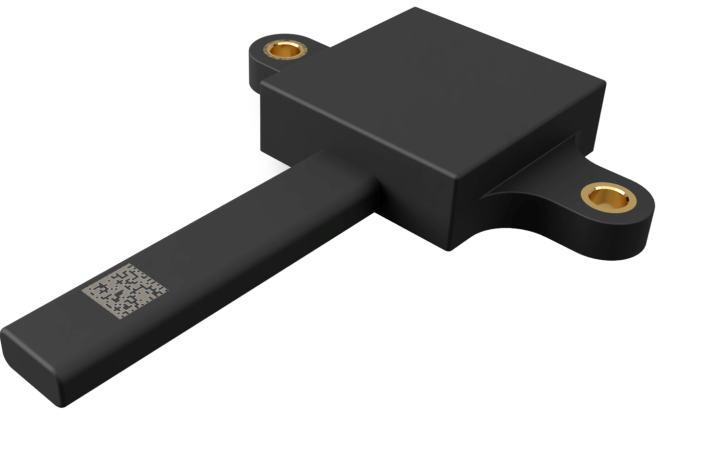
Our position sensors with the inductive measuring principle determine the position of mechanical components without contact and without wear. The so-called target is attached to the moving part of the mechanism and interacts without contact with the stationary sensor system via inductive mechanisms. The sensor and target are each encapsulated against environmental influences, which enables operation in harsh environments.
For example, the position of clutches, dampers and hydraulic cylinders can be measured.
Imbalance sensor
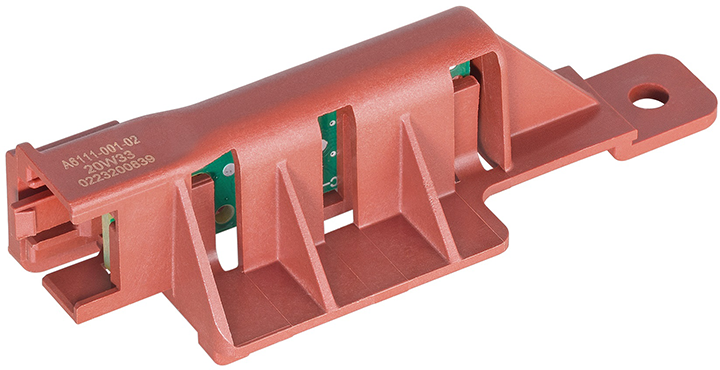
Imbalance can occur in a number of ways, such as when washing is not properly distributed within a washing machine. It may be due to a particular item soaking up an excessive amount of water or several items becoming entangled. While this does not have any negative impact during the normal wash cycle, the powerful forces generated during the spin cycle can prove problematic. As a result, nearly all washing machines now feature an imbalance monitor to prevent damage to the appliance.
Our sensors permanently monitor the weight distribution and the movement of the drum, with the appliance control system evaluating the data and adjusting the speed accordingly. A smart algorithm is then used to redistribute the washing in accordance with the load and thereby resolve the imbalance in the drum.
Force- & Torque-Sensor
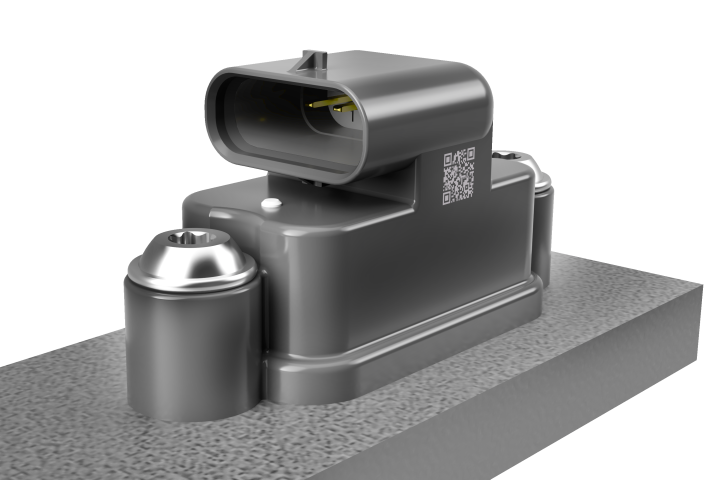
AST‘s inductive Force-& Torque sensors make it possible to use structural components to measure forces and torques. The acting forces and torques lead to minimal deformations of the structure, which can be precisely detected by the sensitive sensors. The measuring principle is based on eddy currents and can detect changes in geometry in the nanometer range. The sensor electronic can be integrated into the sensor element or can be connected via a cable. Especially in high temperature environments it makes sense, to keep the electronic box separated.